OSHA & ANSI
Information
OSHA - Occupational Safety & Health Act
The Occupational Safety & Health Administration, commonly known as OSHA, publiSHEs what are know as "Standards". These Standards outline what the legal responsibility of the Manufacture, the Employer and the worker are. The Standards are Law. Failure to follow these Standards may result in OSHA citations and fines.
- 1910.269 Electric power generation, transmission, and distribution
- (g) (2) Fall protection
- (i) Personal fall arrest equipment shall meet the requirements of subpart M of part 1926.
- Subpart M of Part 1926 - Fall Protection
- 1926.500 Scope, application, and definitions applicable to this subpart (subpart M)
- 1926.501 Duty to have Fall Protection
- 1926.502 Fall Protection System Criteria & Practices
- 1926.503 Training Requirements
- Appendix to Subpart M
- App A Determine Roof Widths
- App B Guardrail Systems
- App C Personal Fall Arrest Systems
- App D Positioning Device Systems
- App E Sample Fall Protection Plans
- 1926-500 Scope & Application
(A) (1) This subpart sets forth requirements and criteria for fall protection in construction workplaces. It does not apply to employees making an inspection or assessment of the workplace prior to work starting or after construction has been completed. - 1926-501 Duty to have Fall Protection
This section sets forth requirements for the employer to provide fall protection for the employee. Employees working 6' or more above a lower level shall be protected from falling by the use of a fall arrest system, safety nets, or a personal fall arrest system.- (2) Sets forth those workplaces, conditions, operations, and circumstances for which fall protection shall be provided except as follows:
- (1) employees working on scaffolds that are covered under subpart L
- (11) employees working on cranes that are covered under subpart N
- (111) employees performing steel erection work that are covered under subpart R
- (1V) employees working on equipment in tunneling operations that are covered under subpart S
- (V) employees working in electrical transition and distribution as covered under subpart V
- (V1) employees working on ladders and stairways which are covered under subpart X
- 1926-502 Fall Protection Systems Criteria & Practices
Sets forth the requirements for installation, construction, and proper use of fall protection as outlined in Subpart M.- (2) Employers shall provide and install all fall protection systems required by this subpart for the employee, with all other pertinent requirements met prior to the work beginning that necessitates the fall protection.
- (20) The employer shall provide for prompt rescue of employees in the event of a fall or shall assure that the employees can rescue themselves.
- 1926-502 Fall Protection Systems Criteria & Practices
- (A) (1) The employer shall provide training for each employee exposed to a fall hazard.
- (A) (2) The employer shall assure that each employee has been trained by a competent person.
- (B) (1) The employer shall verify training by maintaining a written certification record of training for each employee.
Find more information on OSHA Standards here: www.osha.gov
ANSI - American National Standards Institute
The American National Standards Institute is a private, nonprofit organization founded in 1918 which facilitates development of voluntary standards. These standards are not law.
- Z359-1 ANSI Safety Requirements for Personal Fall Arrest Systems, Subsystems, and Components
- 1. Scope, Purpose, Application, Exceptions
- 1.1 Scope - This standard establishes requirements for the performance, design, marking, qualifications, instructions, training, inspection, use, maintenance, and removal from service of connectors, full body harnesses, lanyards, energy absorbers, anchorage connectors, fall arresters, vertical lifelines, and self retracting lanyards comprising personal fall arrest systems for users within the capacity range of 130 to 310 pounds.
- 1.2 Purpose & Application
- 1.2.1 This standard addresses only personal fall arrest systems incorporating full body harnesses.
- 1.2.2 This standard addresses equipment for personal protection against falls from heights and applies to the manufacturers, distributors, purchasers, and users of such equipment.
- 1.2.3 Body belts, window cleaner belts, chest waist harnesses and chest harnesses when used for body support or work positioning are not addressed by this standard.
- 1.2.4 Before any equipment shall bear the mark Z359-1 all requirements of this standard must be met.
- 1.3 Exceptions
- 1.3.1 The requirements of this standard do not address the Construction Industry (SIC Division C), Window Cleaning Belts, & Sports-related Activities.
- 1. Scope, Purpose, Application, Exceptions
- A10-14 ANSI Safety Requirements for Construction and Demolition Operations
- 1. Scope & Purpose
- 1.1 Scope - This standard establishes performance criteria for the manufacturer and use of body belts, harnesses, lanyards, lifelines, rope grabs, and shock absorbers for construction and demolition. It does not include lineman body belts and pole straps, window washers belts, or safety ladder belts.
- 1.2 Purpose - This standard details fall arrest/restraint systems, equipment and methods that shall be used when an employee is exposed to a fall hazard.
- 1. Scope & Purpose
Products
Fall Protection / Safety Training Programs
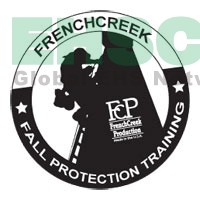
FCP's new training programs are designed to provide awareness, while assisting your company in creating and maintaining a safe and productive work environment. Fall Protection and Confined Space / Rescue training is a necessary and imperative component to a well rounded safety program. Having the proper safety equipment is the first step to safety. The next step is to learn how to properly utilize and care for the safety equipment you have wisely invested in, but don't stop there! It is also necessary for your workers to be trained in recognizing safety hazards, evaluating those hazards, and taking all necessary measures to rectify or protect themselves in the existing work environment.
FCP's field experienced, professional trainers will come to you. We are willing to work with you on-site, or at a location of your convenience, to ensure the best possible training for your company.

A few of the training courses
provided include:
- OSHA Course Training
- Fall Protection Training
- Confined Space Training
- Rescue/Recovery Training
- Ladder & Scaffolding Training
- Tower Climber Training
- Competent Person Training
- Equipment Inspection Training
- Train the Trainer
- Plus so much more!
If your needs aren't listed above, please inquire.
Maintenance,
Inspection & Warnings
Care, Maintenance & Inspection
A well conceived fall protection plan must include proper care and maintenance of all personal protective equipment along with the associated items necessary for a complete system. Training sessions related to care and maintenance should be held at regular intervals depending on the nature of the work. Frequent training sessions are more appropriate for an employer with a transient work force than for an employer with a mature stable work force.
ANSI and OSHA standards require that training be performed by a competent person. The user is responsible for ensuring that he/she knows how to properly inspect, use, store and maintain the equipment.
Storage
Personal protection equipment (harnesses, lanyards, etc.) along with connectors and other related items should be stored in a clean, dry environment free from direct sunlight, dust, excessive heat and harmful chemicals.
Maintenance/Cleaning
Personal protection equipment should be cleaned periodically using a mild detergent and water. Wash with a soft, non-abrasive brush or sponge and allow to air dry after removing the excess water with a dry cloth.
DO NOT put personal protection equipment in a clothes dryer or use a blow dryer. Excessive heat may melt the webbing and alter the strength.
DO NOT use chemicals to clean heavily soiled gear. Chemicals may destroy the webbing.
Frequency of Inspection
User Inspection
Personal fall arrest systems should be inspected by the user before each use. In addition, the user should check before each use to be sure a formal inspection has been performed within the last six months.
Competent Person Inspection
Personal fall arrest systems must be inspected by a competent person at intervals of no more than six months.
Procedure for Inspection
Harnesses, lanyards and synthetic lifelines manufactured from webbing and/or rope (products used in typical fall arrest system).
- Inspect all webbing (straps) and stitching for cuts, fraying, pulled or broken threads, abrasion, excessive wear, altered or missing straps, burn, heat and chemical exposures.
- Inspect all rope for cuts, fraying, pulled or broken strands, abrasion, excessive wear, burns, heat and chemical exposure.
- Inspect all metallic parts (ie. D-rings, snap hooks, buckles, adjusters and grommets) for deformation, fractures, cracks, corrosion, deep pitting, sharp edges, cuts, deep nicks, missing or loose parts, improper function, evidence of burns, excessive heat and chemical exposure.
Corrective Action
User Inspection
When inspection in accordance with stated inspection procedures reveals signs of inadequate maintenance, the harness must be immediately removed from service. Excessive wear and aging are generally not repairable. If detected, immediately remove harness from service. For final disposition, submit the harness to a competent person who is authorized to perform inspections. Contact FrenchCreek Production for further information if necessary.
Competent Person Inspection
The personal protective equipment must be inspected by a competent person other than the user at intervals of no more than six months (The qualifications of a competent person are established by OSHA). If the harness is exposed to sever working conditions, more frequent formal inspections may be required. The frequency of inspection by a competent person should be established by the user's organization based on such factors as the nature and severity of the workplace conditions and exposure time of the equipment. The competent person should perform the inspection following the procedures outlined above. Results should be recorded in the formal inspection log. In addition, the user should check before each use to be sure a formal inspection has been performed within the last six months.
Control of Equipment
The user's organization should establish and enforce a policy and procedure whereby any personal fall arrest system (or parts thereof) are found to be defective, damaged, impact loaded or in need of maintenance be immediately removed from service. Only the manufacturer should make repairs to defective or damaged equipment.
Warnings
FrenchCreek Production does not manufacture, nor do we suggest the use of a body belt only as a component of a fall protection system.
System Types
FALL ARREST SYSTEM (TYPE I)
A fall arrest system may include but is not limited to the following products:
- PERSONAL PROTECTION EQUIPMENT
Full body Harness - will distribute the fall arresting forces over a large portion of the body reducing the chances of internal injury. - CONNECTING DEVICE
Shock absorbing lanyard, lifeline, etc. - means of securing the personal protection equipment to the anchorage point or attachment point. - ANCHORAGE POINT
An I-Beam, Tie Off Strap etc. - an attachment area that will support a minimum of 5000 lbs or more.
POSITIONING SYSTEM (TYPE I OR TYPE II)
A work positioning system is designed to hold a worker in place while giving a hands free approach to his work. A work positioning system must include a secondary system for fall arrest in the event the work positioning system should fail. The following items make up a work positioning system:
- PERSONAL PROTECTION EQUIPMENT
Full body harness - CONNECTING DEVICE (for work positioning)
Re-bar assembly, etc. - a common connector used extensively throughout the construction trade to hold workers in position. - CONNECTING DEVICE (for fall arrest)
Shock absorbing lanyard, lifeline, etc. - a fall arrest connecting device is necessary to protect the working the even his work positioning connector fails, or to protect the worker from a fall while a changing from one work position to another. - ATTACHMENT POINT
An I-Beam, Tie off strap, etc. - any attachment that will support a minimum of 5000 lbs. or more.
SUSPENSION SYSTEM (TYPE I OR TYPE II)
A suspension system is designed to lower and/or raise a worker and support the worker while in that position. Examples include a suspended scaffold or a Bos'n chair supporting a worker on the facade of a building, bridge, etc. The worker must be protected against falling should the work platform fail for any reason. The following are items that make up a suspension system. Your individual suspension system may vary depending upon the work being performed.
- SUSPENSION DEVICE
Suspended scaffold, Bos'n chair or saddle - Items designed for lifting or lowering a worker. - PERSONAL PROTECTION EQUIPMENT
Full body harness or Bos'n chair with full body harness built in - if personal protection equipment is not build into the system, it must be incorporated into the system as an independent item. - CONNECTING DEVICE (for suspension system)
A work line connected from the suspended scaffold or a Bos'n chair to an anchor selected specifically for the suspended system. - CONNECTING DEVICE (for fall arrest)
Lifelines and rope grabs - must commonly this would be a vertical lifeline and rope grab with an anchor point independent of the work platform. - ATTACHMENT POINT
Any attachment that will support a minimum of 5000 lbs. or more.
RETRIEVAL SYSTEM (TYPE I OR TYPE II)
A retrieval system is designed to raise and/or lower workers into and out of confined spaces. The worker should be attached to a retrieval system prior to entering a confined space. If an accident occurs, the worker may be pulled to safety by his retrieval system. Retrieval systems are an important element involved with a rescue, and consideration should be given to the time element involved with the rescue equipment. The following items make up a retrieval system. Your individual retrieval system may vary depending upon the needs of your employees.
- SUSPENSION DEVICE
Suspended scaffold, Bos'n chair or saddle - Items designed for lifting or lowering a worker. - RAISING AND LOWERING DEVICE
Ladder, retrieval/personnel winches, a work line attached to a Bos'n - a means of enabling the worker to enter or exit a confined space. - PERSONAL PROTECTION EQUIPMENT
Full body harness - a worker entering a confined space should be wearing a full body harness to facilitate a rescue. It is not necessary to use an independent full body harness if one is already built into the suspension device. - CONNECTING DEVICE (for personal protective equipment)
Lifelines with rope grabs or recovery winches - a rescue device independent of the raising and lowering system should be attached to the personal protection equipment prior to the worker entering the confined space. - ATTACHMENT POINT
Tripod, davit system, quadpod etc. - any attachment point is necessary for both raising and lowering devices plus the fall arrest/rescue system. The anchorage point must support a minimum of 5000 lbs. or more. A common anchor point for both system could be a tripod designed to attach all of the above items.