Tesla: Is Safety Sacrificed to Production?
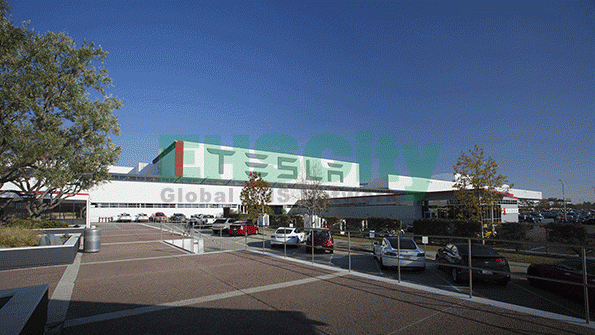
According to reports shared on social media, Musk allegedly sent out an internal email that said in part: "No words can express how much I care about your safety and well-being.”
Worksafe, in “Analysis of Tesla Injury Rates: 2014 to 2017,” notes, “Even though the process of assembling a car has become more technologically advanced, work in an auto plant remains a physically challenging job that carries a higher-than-normal risk of injury.”
According to the report, the average number of nonfatal injuries per 100 full-time workers for the motor vehicle manufacturing industry is double the rate for all industries – 6.7 injuries per 100 workers compared to an average 3.3 for all industries – with Tesla racking up even higher injury rates of 8.1 injuries per 100 workers.
“Over the past several months,” the report continued, “workers at Tesla became increasingly aware of the potential safety hazards at the company’s flagship vehicle plant in Fremont, California.”
Jonathan Galescu is a body repair technician at Tesla who obtained the OSHA Form 300 logs. “The reason we asked for Tesla’s safety log is simple. We see people getting injured in the plant on a regular basis – people who do the same sorts of jobs that we do,” said Galescu. “We want to know – in fact, we need to know – the facts about how often workers are getting injured, and how those injuries are happening. It took us several attempts just to get management to give us the information they’re required by law to provide. It shouldn’t have to be that way. Workers shouldn’t have to risk retaliation just to learn more about safety in the workplace.”
The logs were turned over to Worksafe, and its analysis of Tesla’s injury and illness logs from 2014-2017 found that:
- Tesla’s total recordable incidence rate (TRIR) in 2015 was 31 percent higher than the industry-wide incident rate (8.8 injuries per 100 workers, compared to 6.7 for the automobile manufacturing industry as a whole). The TRIR represents the average number of nonfatal injuries per 100 full-time workers. “This means that workers at the company’s Fremont plant were injured more than the average automobile industry workers,” noted Worksafe.
- Tesla’s total injury rate for 2016 was 8.1 injuries per 100 workers. “While official industry-wide statistics are not yet available for 2016, based on the previous three years of industry data it is very reasonable to expect that the company’s rates will again surpass the industry-wide incident rate, which has stayed relatively constant over time,” the report noted.
- The rate of serious injuries at Tesla’s Fremont plant – those that result in days away from work, restricted duty, or job transfer – was approximately double the industry rate for 2015. This measurement is known as the DART rate (“Days Away, Restrictions and Transfers”). The report noted that the DART rate at Tesla in 2015 was 7.9 compared to the industry average of 3.9. Tesla’s DART rate for 2016 was 7.3, which based on the previous eight years of industry data, it is reasonable to expect will again be higher than the industry rate.
Tesla’s Response
Elon Musk allegedly has requested that every injury be reported to him. In the memo posted to social media, he noted, “It breaks my heart when someone is injured building cars and trying their best to make Tesla successful.”
In that memo, Musk said he’s meeting with the company’s safety team every week and “would like to meet with every injured person as soon as they are well so that I can understand from them exactly what we need to do to make it better. I will then go down to the production line and perform the same tasks that they perform.”
Tesla recently has been touting its improved safety record. In a May blog post titled, “Creating the Safest Car Factory in the World,” the company notes that the United Automobile Workers (UAW) is trying to unionize the Fremont facility, claiming that “safety is an issue the UAW frequently raises in campaigns against companies.”
Tesla cautioned about articles that “downplay or ignore our actual 2017 safety data and instead focus on a small number of complaints and anecdotes that are not representative of what is actually occurring in our factory of over 10,000 workers.”
The company stated in the blog post that the facility has experienced a 52 percent reduction in lost time incidents and a 30 percent reduction in recordable incidents from the first quarter of 2016 to the first quarter of 2017. In addition, through the end of the first quarter of 2017, the factory’s total recordable incident rate is 4.6, which is 32 percent better than the industry average of 6.7, it claims.
While not directly addressing the Worksafe analysis indicating relatively high TRIR rates for 2015 and 2016, Tesla noted in the blog post that, “As we work to achieve our mission, nothing is more important to us than protecting the health and safety of our employees. As we look at our safety record in prior years, we realize that we have not been perfect. No car factory is perfect, but particularly given that Model S and X were the first cars we built at more than tiny volumes, we fully acknowledge that they were not designed for ease of manufacturing – far from it. As would be expected, we have since learned many lessons, including how to improve the production process for the well-being of our colleagues.”
The company mentioned several production changes aimed at creating a safer work environment, including:
- Reducing overtime. Historically, depending on production needs, some Tesla employees worked significant amounts of overtime “because it was necessary for the company to survive,” according to Tesla. In 2016, the company added a third shift to reduce the overtime burden on each team member and to improve safety. “We did this because our employees asked for it, and because it was the right thing to do.”
- As a result of this change, the average number of hours worked by production team members has dropped to about 42 hours per week, and the level of overtime decreased by more than 60 percent. The company hired its first dedicated ergonomist in 2013, and in 2015 established an Ergonomics Team exclusively focused on improving health and safety and reducing ergonomic risk for current and future production.
- In addition to improving the ergonomics involved in building Model S and X, the ergonomics team worked with engineers on the design process for the Model 3. The team created simulations that showed them where reaching or bending by employees was most likely to occur, which in turn allowed them to redesign the equipment and the car to eliminate these issues as much as possible.
- Each department now has a safety team that meets regularly to increase safety awareness and recommend improvements, many of which already have been implemented, according to the company.
Tesla claims it is “continuing to establish health and safety management procedures to scale with our operational growth.”
As Musk allegedly wrote in the internal memo, “At Tesla, we lead from the front line, not from some safe and comfortable ivory tower. Managers must always put their team’s safety above their own.”
2017 Numbers “Do Not Paint A Complete Picture”
The Worksafe report acknowledges the improved injury and illness data reported by Tesla for the first quarter of 2017, but notes, “These figures are only for the first several months of 2017, may be incomplete and do not paint a complete picture of Tesla’s safety record. Nor are injury rates – also referred to as ‘incidence rates’ – the only way to evaluate a company’s track record on safety.”
The group also called into question the reliability of Tesla’s injury and illness reporting. Worksafe claims that Tesla made significant revisions to its 2016 data, and two versions of the 2016 OSHA 300 logs were provided to workers, one dated Feb. 1 and one dated May 3.
In the annual injury and illness data that Worksafe claims Tesla submitted to Cal/OSHA on Feb. 1, the company allegedly reported 705 reportable injuries, including 139 injuries resulting in the injured worker missing days of work, and 507 injuries requiring the worker to be placed on restricted duty or be temporarily transferred to another position (collectively “restricted duty”). These injuries resulted in workers missing 4,468 days of work and spending 18,035 days on restricted duty.
On May 3, Worksafe claims Tesla amended its 2016 report, and the new report listed 840 reportable injuries, 135 more than previously reported. The number of injuries involving days away from work nearly doubled to 267, and the aggregate number of work days missed due to injuries tripled, from 4,468 to 13,608. While the amended report reflected 493 restricted duty cases, a slight decline, the number of restricted duty days reported almost doubled, from 18,035 to 33,314.
EHS Today contacted Cal/OSHA about the claims made by Worksafe regarding Tesla's amended 300 logs and received this response from a Cal/OSHA spokesperson in return:
"Cal/OSHA cannot comment on how often companies amend their Log 300. Employers are required to maintain a Log 300 and the criteria needed in the log is outlined in Title 8 section 14300.7 of the California Code of Regulations.
The Log 300 is not submitted yearly or regularly to Cal/OSHA. A copy of the Log 300 can be requested by Cal/OSHA during the course of an inspection.
The WorkSafe report 'Analysis of Tesla Injury Rates: 2014 to 2017' mentions Tesla submitting its ‘Log 300 data to Cal/OSHA on February 1 2017.’ However, Cal/OSHA has no record of receiving or requesting this information from Tesla on this date. February 1 is the date that employers must post the Log 300(a) in their workplace for employees to see. The Log 300(a) is the summary of workplace injuries and illnesses."
Putting Faces to Numbers
Worksafe noted that by law, companies need only report the first 180 days an employee spends on medical leave or on job transfer for light duty. The agency claims this becomes significant to the total number of days missed due to injuries and restricted duty days when Worksafe analyzed the cases of two employees.
Production associate Charlotte (Charley) Briese claimed that she has been injured three times, the first in July 2015. Her position at that time required her to pull down a hanging drill three times a minute for 12-to-16 hours a day. On a 12-hour shift, she made the same motion approximately 2,200 times a day, or 15,000 times a week, or 60,000 times a month. “After six months, I had severe tendonitis in my elbow and wrist,” said Briese, who was placed on medical leave until October 2016.
In April 2016, she again was injured when a torque gun slipped from her hand. It crushed her thumb, she said, and she was transferred to light duty in the plant for approximately a month.
When she returned from light duty, she was rotated to a new station building the side view mirror on the Model S and putting the skull caps on the mirrors. According to Briese, “It takes a lot of strength to put them on, and it’s very fast paced. I was uncomfortable starting on it right away, after being on light duty for a month, and I raised my concern to my lead.”
She claims that she was told that if she “didn’t feel comfortable doing it, I should go home and not come back. So I stayed.”
After three days, Briese claims she could not lift her arms above her head. She was sent to the nurse, who changed her work restrictions to show that she should keep her elbows at her waist and not lift more than 10 pounds. Eventually, Briese was placed on a leave of absence in May 2016, and her pay was reduced. That leave of absence has continued into 2017.
When Alan Ochoa, another production associate, started working at Tesla in 2014, his job was to assemble door panels, a job that involved spot welding, operating a hand drill and installing sound insulating materials. “I was the only one who was under 30 years old, one of the only ones able to keep up with the line,” he said. “But we started falling behind. The number one rule is that you can’t stop the line. They call it the Money Line – if you stop it for 10 minutes they say it’s a million dollars out the door.”
The fast past took its toll on Ochoa, who claims that he noticed he was having a hard time maintaining his grip. Soon, he started noticing pain in his wrists and hands.
When he talked to management about the pain he was experiencing, he was transferred to a job assembling door handles. This “light duty” work exacerbated his pain, he claims, adding “Tesla’s workers’ compensation doctors misdiagnosed me twice. They told me it was a strain, gave me ibuprofen and sent me back to work. That didn’t work. Eventually I was diagnosed with carpal tunnel in both wrists.”
Ochoa was placed on medical leave in May 2015 and had surgery for carpal tunnel. He returned to Tesla for one month in 2016, but the job to which he was assigned required him to type on a laptop. After one week, he had a flare up that lasted three weeks, and he was removed from the light duty program again. “To be honest,” said Ochoa, “I don’t know what my future is.”