While nearly every company will say that safety is a priority, are they really doing what they can to promote safe operations? Companies may possess a strong and sincere commitment to safety, but all too often, the approach is reactive, with leaders responding to incidents hoping to stop them from recurring.
For those companies that find themselves in such a position, the highest safety priority is the current incident. They find that changes only happen after the incident occurs, and safety culture returns to what it was before the incident. The organization can feel overwhelmed by new, reactive safety rules and requirements, some of which seem to have little connection to a broader purpose.
Promoting safe operations should not feel like a game of “whack-a-mole” in which incidents are dealt with as they happen. It’s much better to anticipate and prevent incidents. Companies can know when and where the next incident is likely to occur; they can know which hazards deserve more attention than others and they can involve their workers, empowering them to be proactive in anticipating and avoiding hazards.
Managing Risk, Not Just Safety
Most companies utilize a safety management system that includes various components which act as barriers to prevent a hazard from becoming an incident. These components include an analysis of potential hazards, permits to operate machinery, procedures for operations and past incident investigations, to name a few.
Unfortunately, these components are not perfect – they all have defects of some kind. This is illustrated in the “Swiss cheese” model shown in Figure 1. When the defects in the layers line up (holes in the Swiss cheese) hazards can become incidents. The object of many safety activities is to respond to incidents, and try to close the holes in the layers of Swiss cheese.
Figure 1
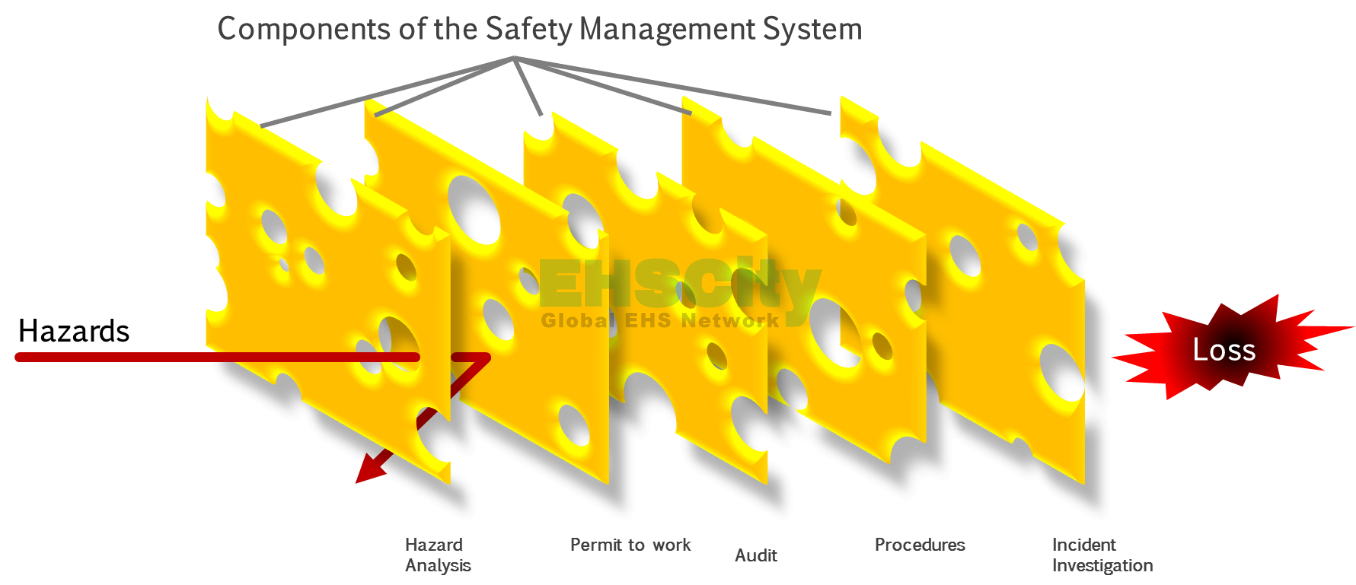
(“Swiss Cheese Model” is from “Human Error: Models and Management,” J. Reason, British Medical Journal, 2000)
An alternate approach to closing the holes is to think beyond the hazards and consider associated risks. Taking the time to recognize all risks that exist in a company’s operations, the conditions in which they occur and implementing steps to mitigate them can significantly improve safety performance. Risk is the quantification of both the likelihood and the potential consequence of a given hazard. once quantified, risks can be prioritized by plotting them on a graph. (See Figure 2)
For purposes of such an analysis, DuPont Sustainable Solutions (DSS) associates each hazard (and its risk) with an activity. The frequency of the activity (number of times it occurs in a year) is referred to as the “Opportunity Frequency” (shown as a diamond in Figure 2). Next, it is necessary to quantify how often something goes wrong, increasing the chance that the hazard will cause an incident. Most companies define a near miss as an opportunity for the incident to occur, under slightly different circumstances.
Near miss reporting is strongly encouraged as a way to learn from “near incidents” through usual incident investigation methods. When DSS started to refer to “near incidents” as near misses, operators and mechanics became discouraged, thinking someone would eventually try to get them to report all near misses. To avoid this issue, DSS labeled “near incidents” as “Oops!” events, and encouraged operators and mechanics to define the “Oops!” frequency. Upon doing so, it was alarming to see the high frequency with which “near incidents” occur.
once the Frequency is defined, the Potential Consequence must be defined. DSS assigns “buckets” for the Potential Consequence (First Aid, Recordable, Lost Time, Fatality, etc.). With Frequency and Potential Consequence defined, the Graph looks like Figure 2.
Figure 2. Risk Frequency Plot
Figure 2 shows a small sample of commercial data. Compare the points labeled “P-6” and “P-8”. They have similar Opportunity Frequencies (about 30,000 times per year), but very different “Oops!” Frequencies and Potential Consequences. P-6 has an “Oops!” Frequency of 2,500 times a year, and is a potential fatality. P-8 has an “Oops!” frequency of 1 time per year, with potential for multiple fatalities. A quick scan of this type of graph reveals which risks companies will want to address first. In this instance, P-6 warrants immediate attention.
This kind of risk determination provides a fundamental basis for a company to determine which risks most warrant mitigation efforts, predict which work activity most likely is to experience the next incident, and then allocate resources accordingly. Over time, as the highest risks are reduced, effort can shift to lower risks. It also is a good idea to look for hazards and risks that have been overlooked previously.
Adjust Your Thinking to Consider Risk
Changing existing behavior within a company to anticipate risks requires workers, managers and executives to add risk thinking to their safety paradigm. (See Figure 3) It’s not that the safety principles listed in figure 3 are wrong, they just don’t tell the whole story. The first point is to understand that risk can never totally be eliminated. This may seem to contradict the statement “All incidents can be prevented.” It does not. By understanding that risk always is present, workers more likely are to maintain hazard awareness and act more safely by anticipating situations that present potential for an incident to occur.
Figure 3. Safety Thinking vs. Risk Thinking
Clearly, management is responsible for both safety performance and risk reduction. But the last two points in the “Risk Thinking “column in Figure 4 interact, and are critical to this discussion. DSS’ work in this area has shown that effective risk management requires the involvement of the employees who do the work. Employees operating equipment and machinery know where hazards and risks exist, and how often they almost have an incident. It is common for workers to eventually identify an “Oops!” frequency that is much higher than anyone might have previously guessed. While management is responsible for risk reduction, they can only do so effectively with worker involvement.
The fortunate byproduct of worker involvement is increased hazard and risk awareness. When workers are involved in identifying hazards, quantifying risks and reducing risks, they are more aware of the hazards and risks in their work.
Companies that want to improve their safety performance actively should manage risks. By measuring and quantifying the many risks that exist throughout the organization, companies are better able to anticipate, prioritize and mitigate those opportunities that most likely are to lead to an incident. It requires that everyone in the company change their outlook to be aware that risk always is present and alert to situations that could lead to a potential incident. By endeavoring to manage risk, companies will find they operate even more safely.
Donald Byrne is program manager with DuPont Sustainable Solutions. Ward Metzler is a principal with DuPont Sustainable Solutions. DuPont Sustainable Solutions (DSS), a business unit of DowDuPont Specialty Products, is a provider of world-class operations consulting services to help organizations transform and optimize their processes, technologies and capabilities. DSS is committed to improving the safety, productivity and sustainability of organizations around the world. Additional information is available at: www.sustainablesolutions.dupont.com.